At Wuxi Repicea, we specialize in providing high-performance heat exchangers for a variety of industries. In this blog, we will discuss the key pros and cons of silicon carbide tube heat exchangers and explore common applications for these robust devices.
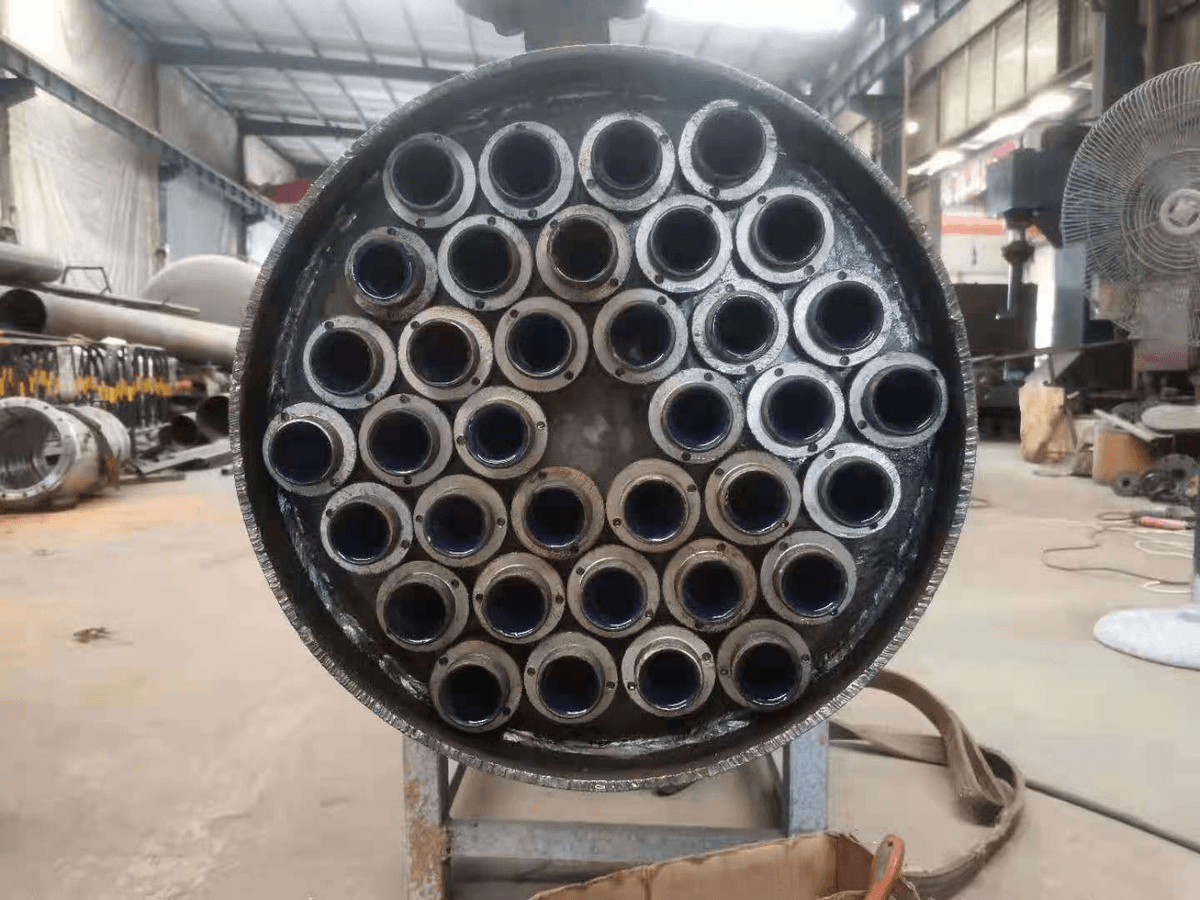
- High-Temperature Resistance
Silicon carbide (SiC) is known for its excellent high-temperature resistance. With a melting point of around 2,700°F (1,482°C), it’s ideal for applications involving extreme heat, such as in the chemical and petrochemical industries. - Superior Corrosion Resistance
SiC offers outstanding corrosion resistance, making it an excellent choice for applications where fluids can be highly corrosive. This resistance helps extend the lifespan of the heat exchanger and minimizes maintenance costs over time. - Long Service Life
Silicon carbide is a highly durable material that can withstand prolonged use in harsh environments. This makes SiC tube heat exchangers a cost-effective option in the long run, as they often outperform other materials in terms of lifespan. - Lightweight
Despite its strength, silicon carbide is a relatively lightweight material, which facilitates easy transportation and installation of the heat exchangers in industrial facilities.
Disadvantages of Silicon Carbide Tube Heat Exchangers
- High Cost
Silicon carbide is a premium material, which makes the initial cost of these heat exchangers relatively high. This can be a drawback for applications with tight budgets. - Brittleness
SiC is a brittle material and may fracture or crack under impact or vibration. This is a critical consideration when handling or installing the heat exchangers in environments prone to physical stress. - Specialized Manufacturing Process
The production of silicon carbide tube heat exchangers requires a specialized manufacturing process, which can make them more difficult and expensive to produce compared to other types of heat exchangers.
Common Applications for Silicon Carbide Tube Heat Exchangers
Given the advantages and limitations of silicon carbide tube heat exchangers, they are best suited for specific applications that require durability, high-temperature resistance, and corrosion protection. Some common applications include:
- Chemical and Petrochemical Industries
Silicon carbide tube heat exchangers are frequently used in the chemical and petrochemical industries, where they handle high-temperature fluids and corrosive materials. - Power Generation
In the power generation industry, SiC heat exchangers are used to manage the transfer of heat between high-temperature fluids, ensuring efficient energy production. - Oil and Gas Industry
The oil and gas industry benefits from silicon carbide heat exchangers for heat transfer in processes involving high-temperature fluids. Their durability and resistance to harsh conditions make them ideal for these applications.
Conclusion: Is Silicon Carbide the Right Choice for You?
While silicon carbide tube heat exchangers offer exceptional performance in high-temperature and corrosive environments, their high cost and brittleness may not make them suitable for every application. It's crucial to carefully evaluate your specific needs and consider the advantages and disadvantages before choosing a heat exchanger solution.
If you're considering the use of silicon carbide heat exchangers for your operations, Wuxi Repicea can help guide you through the decision-making process and provide customized solutions to meet your industry’s requirements. Contact us today for more information on how we can assist with your heat exchanger needs.