·
Abstract
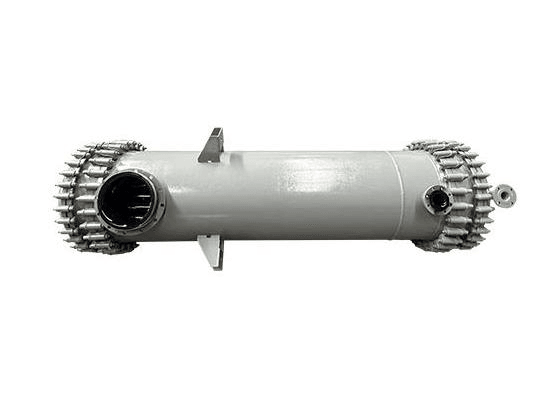
1. Classification by Heat Transfer Mode
1.1. Tubular Heat Exchanger
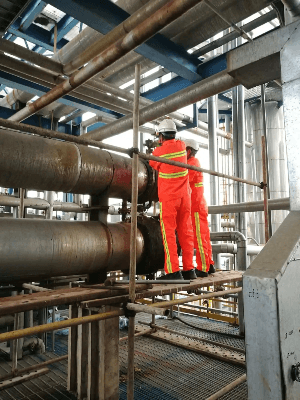
1.2. Regenerative Heat Exchanger
1.3. Fluid - connected Indirect Heat Exchanger
1.4. Direct - contact Heat Exchanger
1.5. Compound Heat Exchanger
This is a heat exchanger that combines multiple heat transfer methods, integrating the advantages of different types of heat exchangers.
2. Classification by Application
2.1. Heater
Used to heat the fluid to the required temperature, such as in the heating process of raw materials in some industrial production processes.
2.2. Pre - heater
Typically used to pre - heat the fluid before the main heating process to enhance energy utilization efficiency.
2.3. Superheater
2.4. Evaporator
Used to evaporate liquids. For example, in a refrigeration system, the evaporator can make the refrigerant liquid evaporate and absorb heat.
3. Classification by Structure and Detailed Descriptions of Each Type
3.1. Shell and Tube Heat Exchanger (Highlighted)
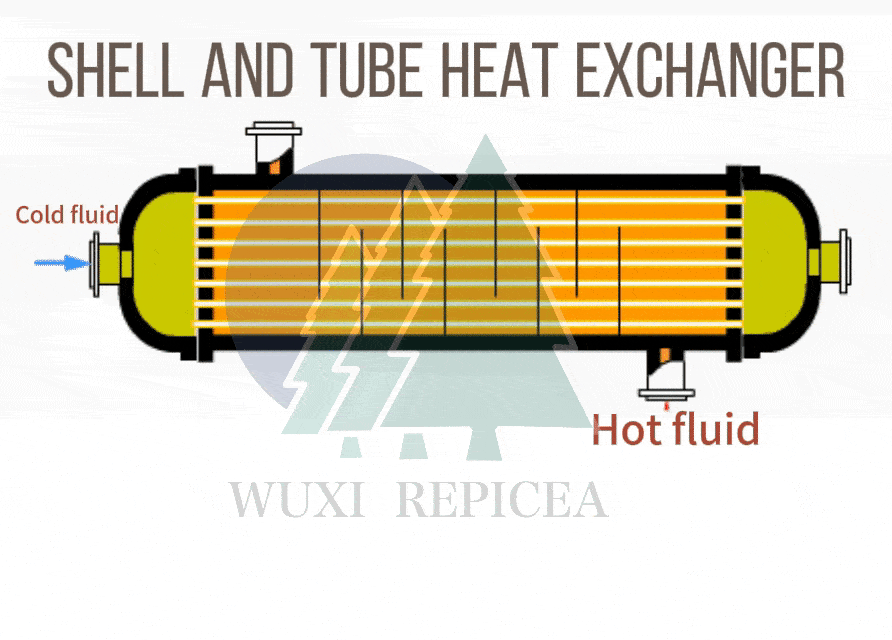
- Working Principle: When the hot fluid flows through the tube - side and the cold fluid through the shell - side, heat is transferred from the hot fluid to the cold fluid through the tube wall. Vice versa, the cold fluid can be in the tube - side and the hot fluid in the shell - side.
- Advantages: Simple and compact structure with relatively low cost. It has a wide range of applications, can handle various fluids, and shows good adaptability to fluid pressure, temperature, and flow conditions. It can withstand relatively high pressure and temperature and can operate stably in some high - pressure and high - temperature industrial environments.
- Disadvantages: The outside of the tubes cannot be mechanically cleaned, and there is a significant temperature - difference stress between the tube wall and the shell wall, which may affect the service life of the heat exchanger.
3.2. Floating - head Heat Exchanger
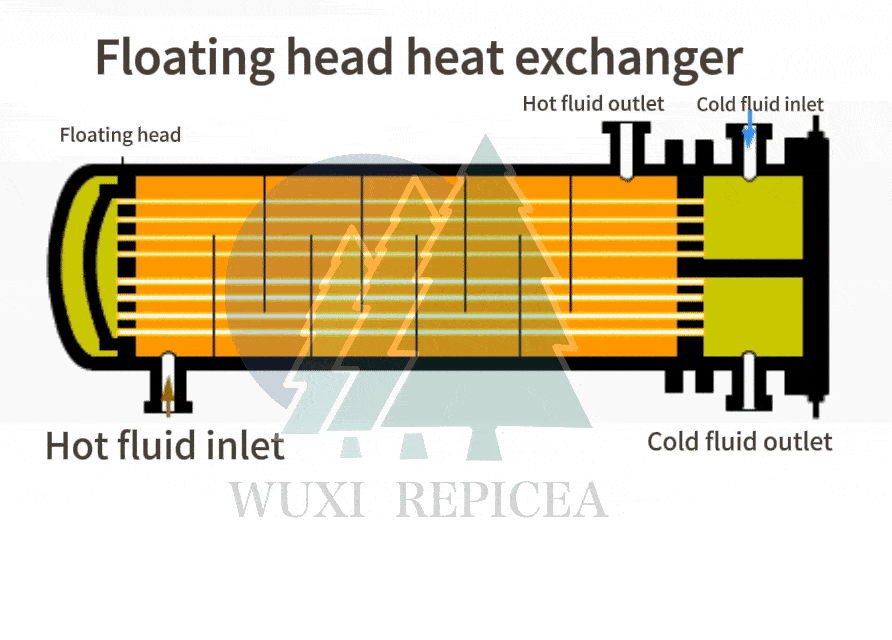
- Structural Features: One of the tube sheets at both ends is not connected to the shell and can float freely in the tube length direction. When the shell and the tube bundle have different thermal expansions due to temperature differences, thermal stress can be eliminated.
- Working Principle: The hot and cold fluids enter through different inlets, exchange heat through the partition wall between the tube bundle and the shell, and then exit through their respective outlets.
- Advantages: Can eliminate temperature - difference stress and is capable of operating under high - temperature and high - pressure conditions. Generally, the temperature can be up to 450 degrees Celsius, and the pressure can be up to 6.4 MPa. The heat exchanger tube bundle can be removed for cleaning, making it suitable for applications where fouling is likely or the tube - side is prone to corrosion.
- Disadvantages: The structure is complex, and the small floating - head is prone to internal leakage. There is a high consumption of metal materials, and the cost is approximately 20% higher than that of ordinary heat exchangers.
3.3. U - tube Heat Exchanger
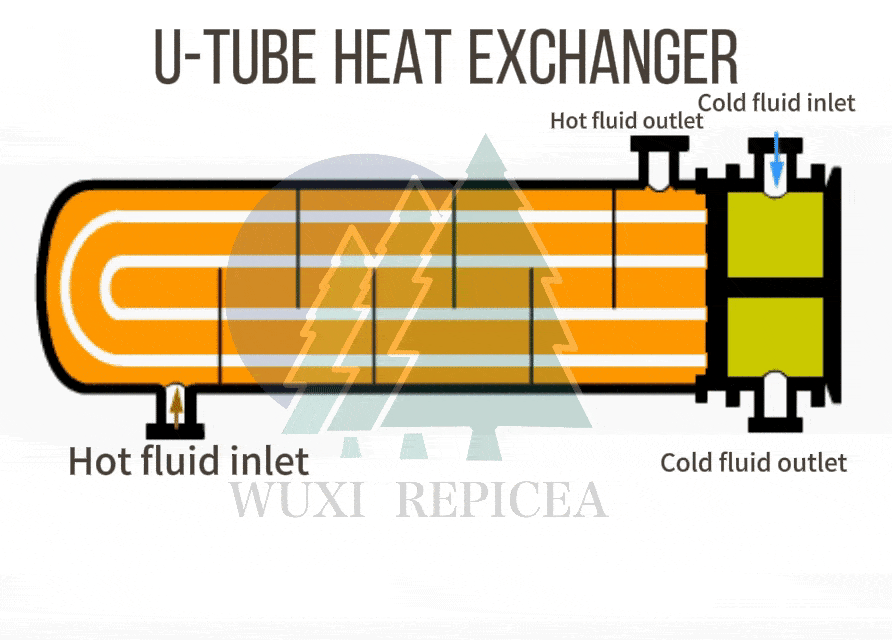
- Structural Features: Each tube is U - shaped and fixed on the same - side tube sheet. Each tube can expand and contract freely to eliminate thermal stress. The tube - side has a double - tube - pass configuration with a long flow path.
- Working Principle: The hot and cold fluids enter through different inlets and exchange heat inside and outside the U - tube before exiting through their respective outlets.
- Advantages: The tube bundle can expand and contract freely, and there is no thermal stress between the tube and the shell. The double - tube - pass tube - side has a long flow path, resulting in good heat exchange efficiency and strong pressure - bearing capacity. The tube bundle can be withdrawn from the shell for easy maintenance and cleaning. The structure is simple, and the cost is low.
3.4. Immersed Coil Heat Exchanger
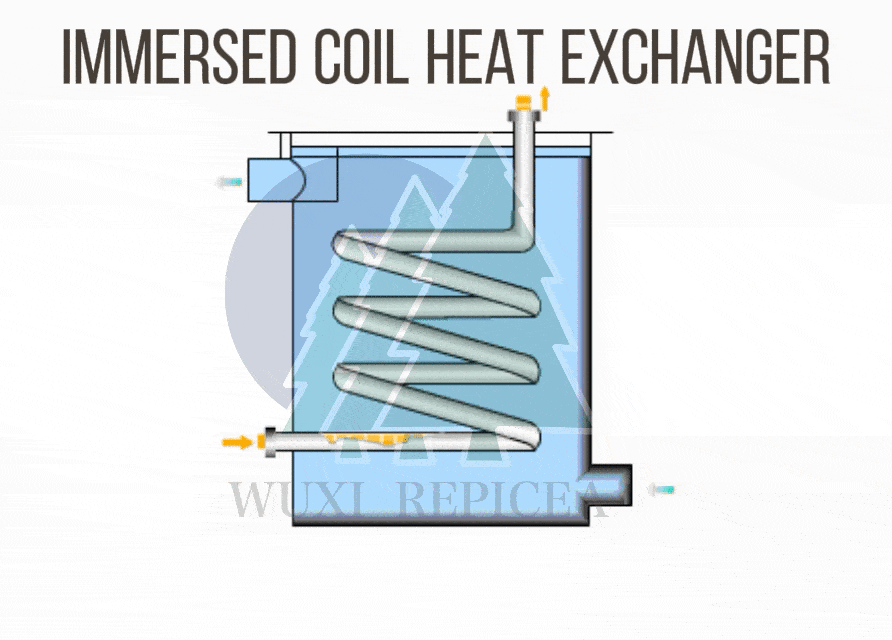
- Structural Features: Utilizes a serpentine tube as a heat transfer element.
- Working Principle: Depending on the cooling method of the fluid outside the tube, the coil heat exchanger can be divided into immersed and spray types. In the immersed type, the fluid outside the tube surrounds the coil for heat exchange.
- Disadvantages: The equipment is bulky, consumes a large amount of materials, and requires more metal per unit of heat transfer.
3.5. Spray - type Coil Heat Exchanger
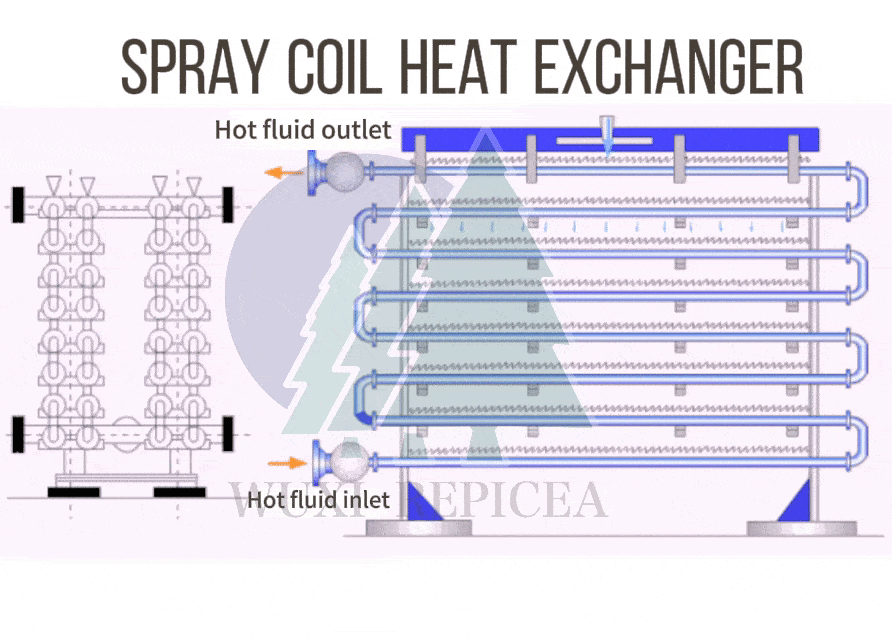
- Structural Features: Similar to the immersed coil heat exchanger, but equipped with a spraying device for spraying the fluid outside the tube.
- Advantages: The heat transfer effect is better than that of the immersed type, the heat transfer area is large and adjustable, and it is convenient for inspection and cleaning.
- Disadvantages: The spraying may be uneven. It is mainly used for cooling the fluid inside the tube and is often installed in outdoor areas with good air circulation.
3.6. Double - pipe Heat Exchanger
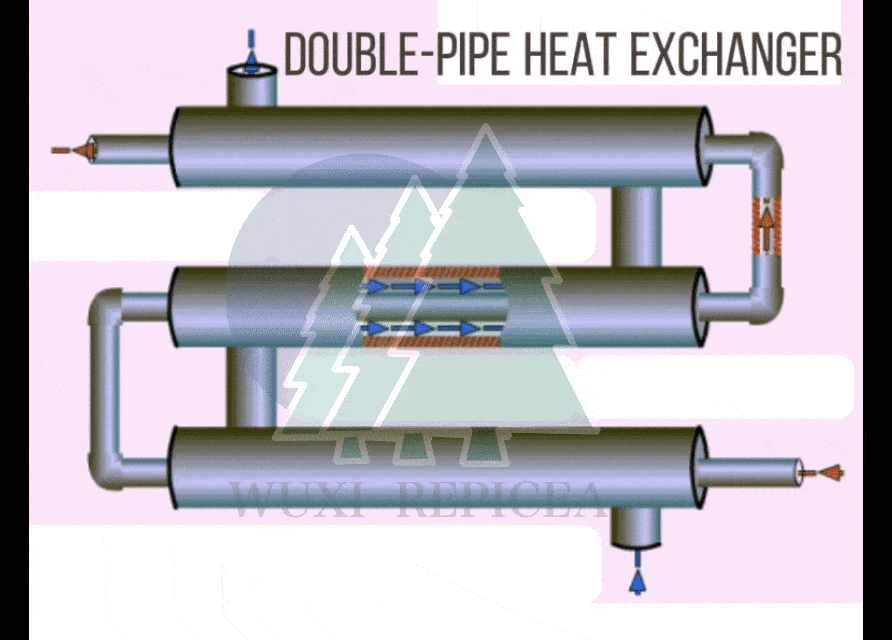
- Working Principle: The hot fluid flows in the annular space between the outer surface of the inner pipe and the inner surface of the outer pipe, and the cold fluid flows in the inner pipe. Heat is exchanged between the two fluids through the pipe wall.
- Advantages: Large heat exchange area and high heat transfer efficiency.
- Disadvantages: Repair, cleaning, and disassembly are troublesome, and leakage is prone to occur at detachable connections.
3.7. Spiral - plate Heat Exchanger
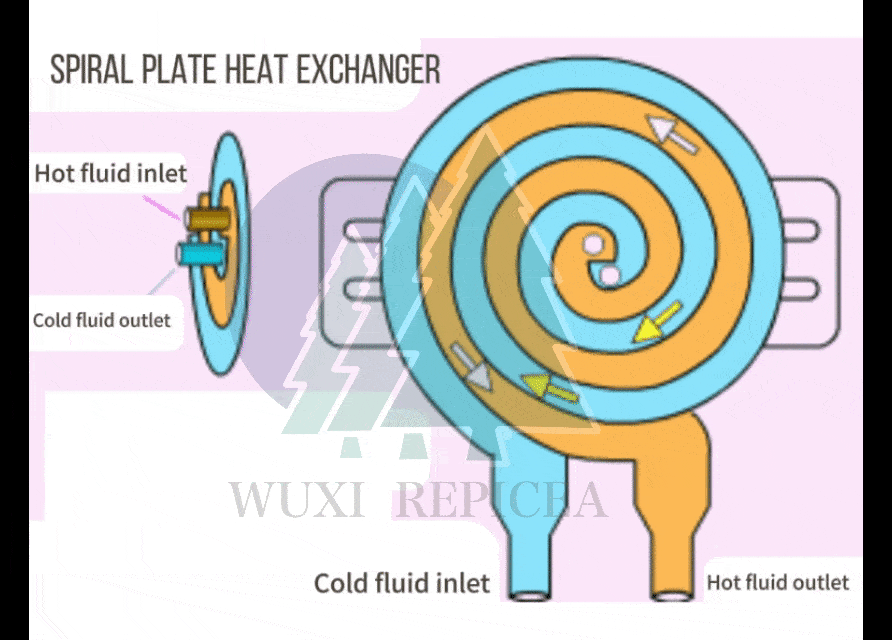
- Structural Features: Formed by parallel steel plates creating staggered spiral flow channels with covers on both sides. The cold and hot fluids flow in the two respective flow channels.
- Working Principle: The cold and hot fluids exchange heat through the steel plate walls as they flow through the spiral flow channels.
- Advantages: Good heat transfer efficiency, stable operation, can be used in multiple units, high heat transfer efficiency, strong operation reliability, and low resistance.
- Disadvantages: Demands high - quality welding, is difficult to repair, is heavy, has poor rigidity, and is challenging to transport and install.
3.8. Heat Exchanger with Expansion Joint
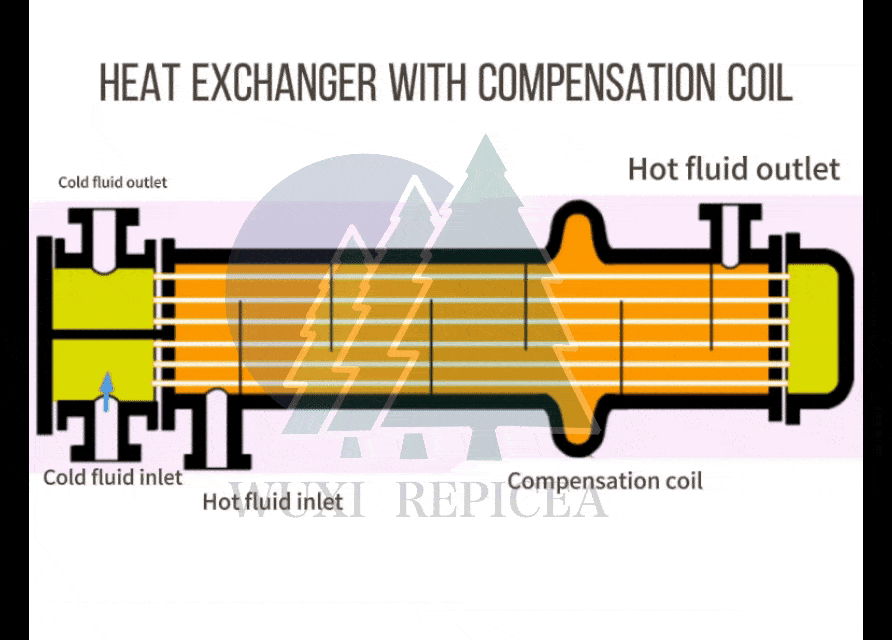
- Structural Features: Equipped with an expansion joint. When the fluid undergoes high - temperature heat exchange and there is significant thermal stress in the tube - shell side, the expansion joint can eliminate this stress. When the shell and the pipeline have different expansions, the expansion joint undergoes elastic deformation, stretching, or compression to adapt to the different thermal expansion degrees of the shell and the tube.
- Working Principle: The hot and cold fluids enter through different inlets, exchange heat through the partition wall between the tube bundle and the shell. During high - temperature heat exchange, the expansion joint functions to eliminate thermal stress, and then the fluids exit through their respective outlets.
- Advantages: Applicable in situations where the temperature difference between the two fluids is not greater than 70 °C and the shell - side fluid pressure is not higher than 600 kPa, effectively eliminating thermal stress.
3.9. Heat Pipe Heat Exchanger
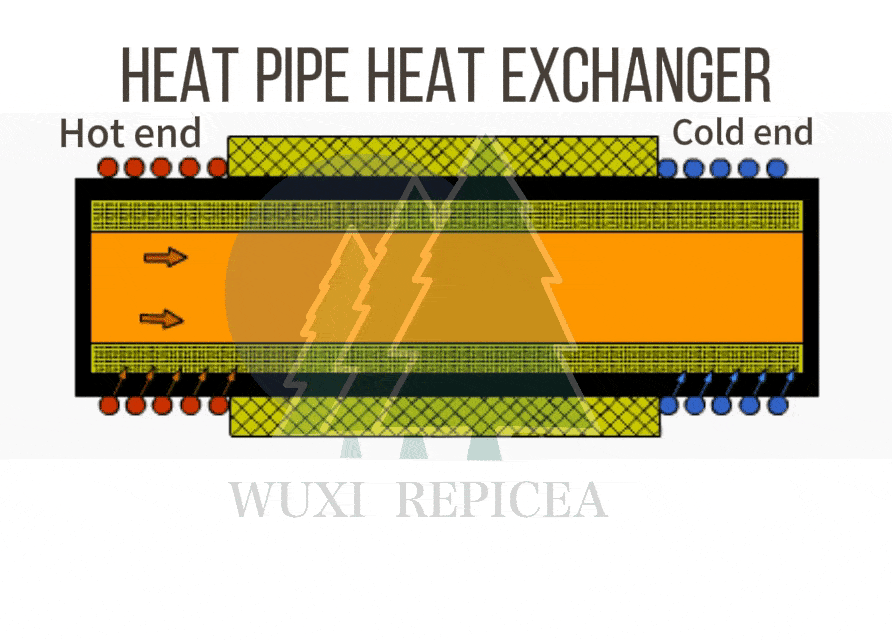
- Structural Features: A sealed metal tube with the inner wall covered by a core network made of capillary structure material. The interior is hollow and contains a certain amount of heat carrier (such as ammonia, etc.).
- Working Principle: The heat carrier is vaporized and flows to the cold end. At the cold end, the vapor is condensed, releasing the latent heat of vaporization and heating the cold fluid. The cold liquid then flows back to the hot end, and this process repeats.
3.10. Jacketed Heat Exchanger
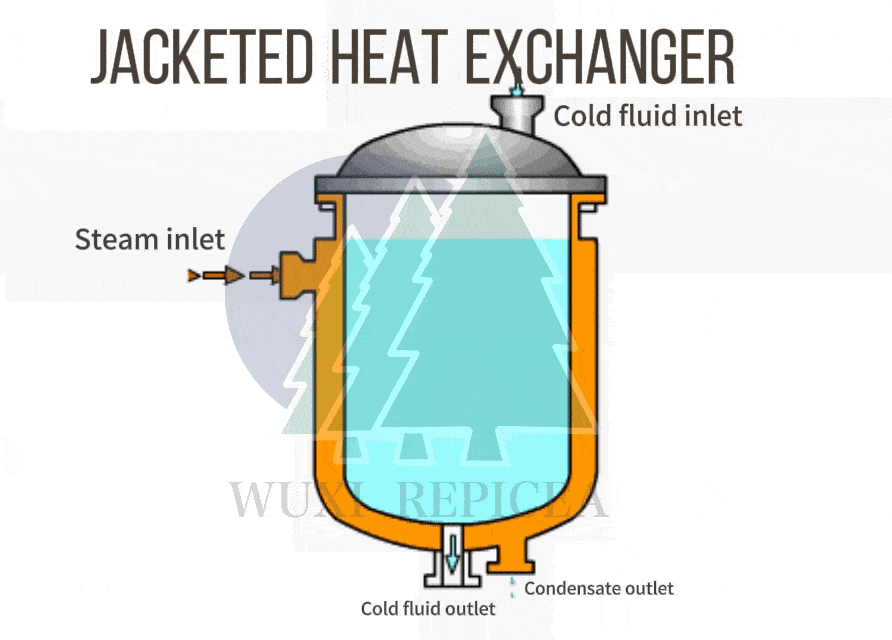
- Structural Features: Has a jacket structure, and the hot fluid transfers heat to the cold fluid through the jacket.
- Working Principle: The hot fluid flows in the jacket, and the cold fluid flows in the container within the jacket. Heat is exchanged through the jacket wall.
- Advantages: Simple structure, easy to manufacture and transport.
- Disadvantages: The heat transfer area is limited, and the heat transfer coefficient is not high. A stirrer or coil can be added to increase the heat transfer coefficient.
3.11. Plate - fin Heat Exchanger
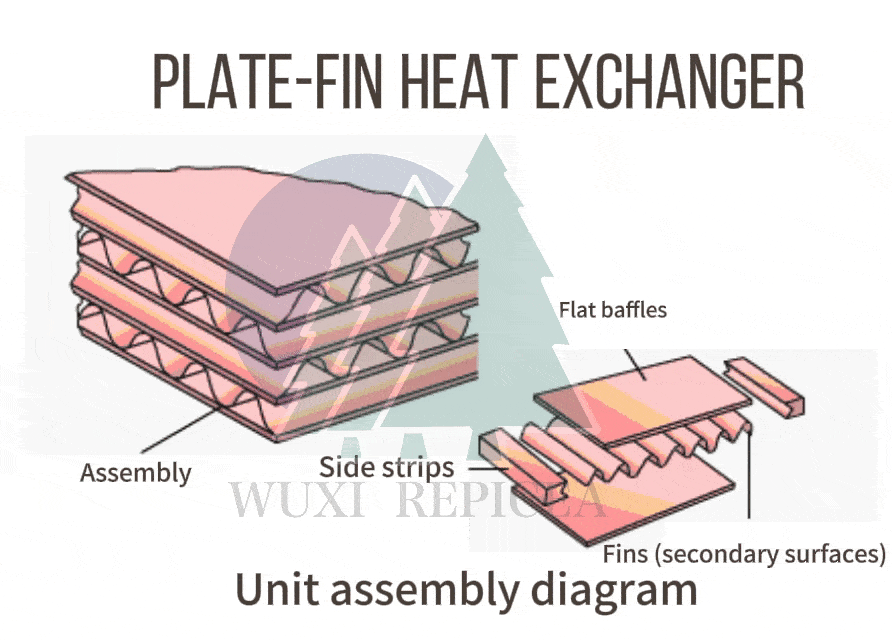
- Structural Features: Composed of plates, fins, and strips to form unit bodies. Multiple unit bodies are assembled into an assembly through forward or cross - flow, and then a header with a collecting outlet is welded to the assembly.
- Working Principle: The hot and cold fluids flow in the channels formed by the fins and plates respectively and exchange heat through the fins and plates.
- Advantages: Compact and lightweight structure, high heat transfer coefficient, and strong applicability.
- Disadvantages: Demands high - quality manufacturing, has a complex process, is prone to clogging, is not corrosion - resistant, and is difficult to repair and maintain. Thus, it is only suitable for clean liquids.
3.12. Gas Cooling Tower
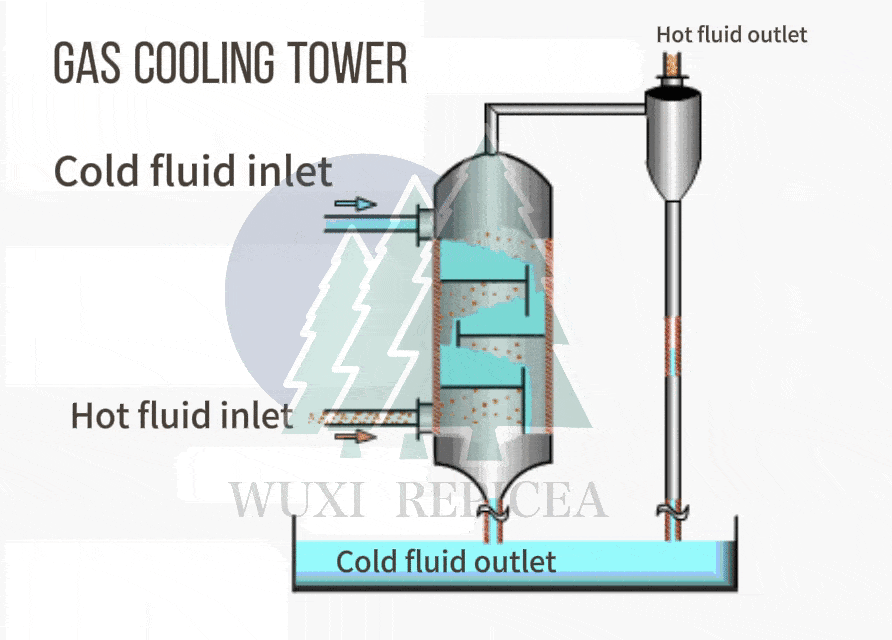
- Structural Features: Hot gas enters from the bottom of the tower and contacts water in the tower for heat transfer through bubbling.
- Working Principle: During the upward movement of the hot gas, it fully contacts the water and transfers heat to it. The outlet at the top of the tower is the cooled gas, and the outlet at the bottom of the tower is the heated water.
- Advantages: Can achieve efficient gas cooling.
- Disadvantages: Demands high - precision control of the flow rates of gas and water to ensure good heat transfer effect.
3.13. Thermal Storage Chamber
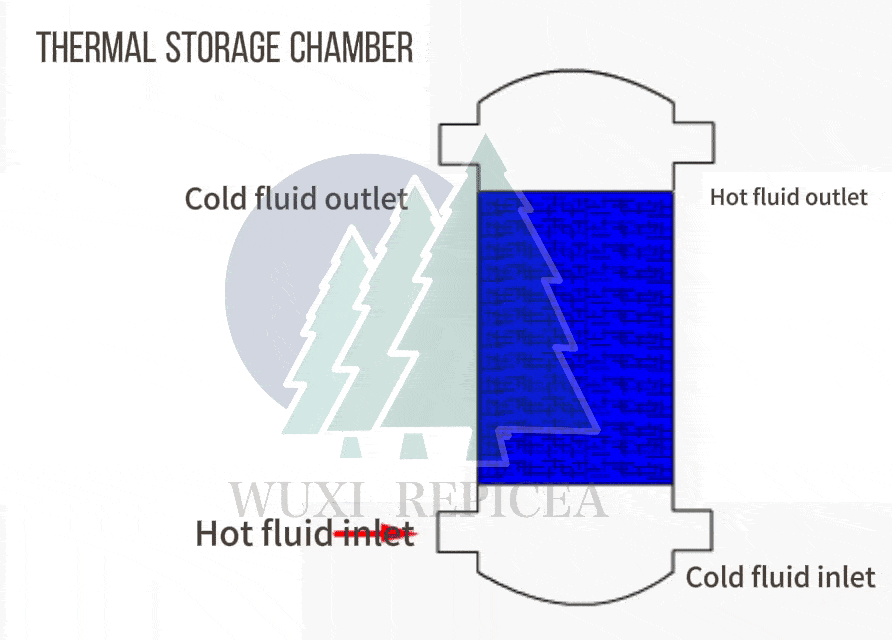
- Structural Features: Incorporates checker bricks or other heat - storage media.
- Working Principle: The hot fluid transfers heat to the checker bricks first, and then the checker bricks transfer the heat to the cold fluid. The hot and cold fluids are not in direct contact but transfer heat through the heat - storage medium.
- Advantages: Enables heat storage and transfer, thereby improving energy utilization efficiency.
- Disadvantages: The heat - storage medium requires regular maintenance and replacement to ensure good heat transfer performance.
3.14. Bathroom Warm - water Heating (Direct - contact Heat Exchanger)
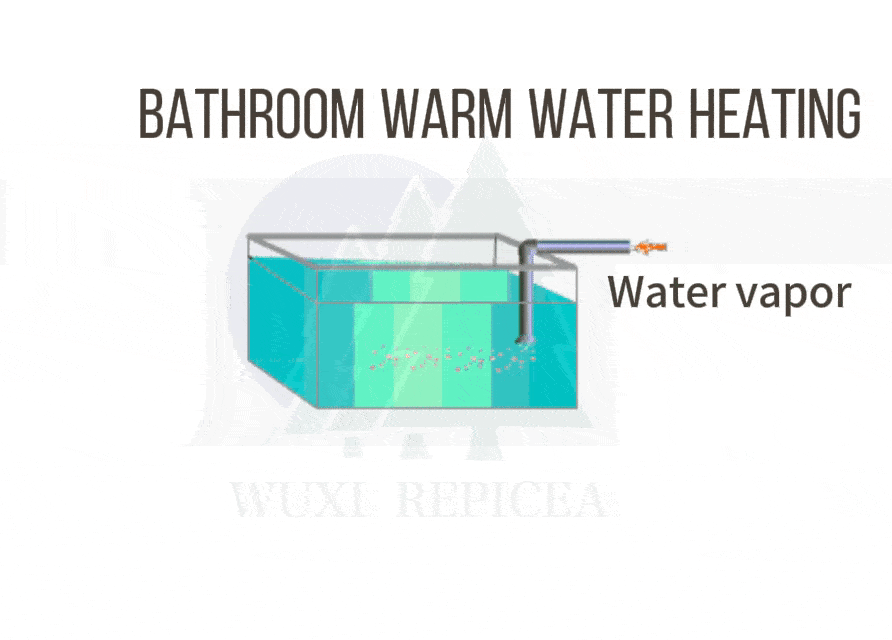
- Structural Features: Steam is directly introduced into a clear - water pool.
- Working Principle: The latent heat of condensation of the steam is directly transferred to the cold water to achieve warm - water heating.
- Advantages: Simple structure and high heating efficiency.
- Disadvantages: Only suitable for applications with low water quality requirements, such as bathrooms.
3.15. Energy - storage Heat Exchanger
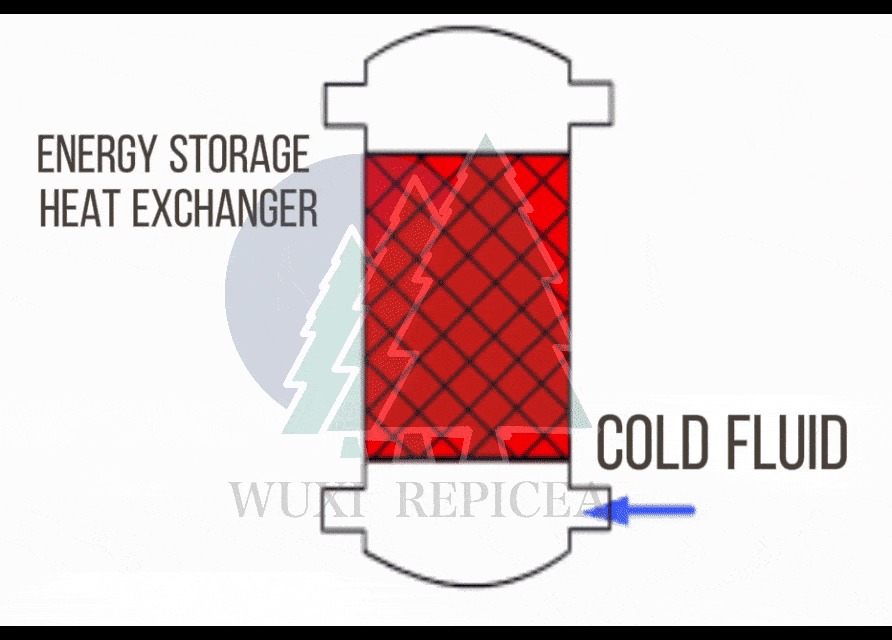
- Structural Features: Usually contains an energy - storage medium, such as phase - change materials, for heat storage.
- Working Principle: When there is excess heat, the heat is stored in the energy - storage medium. When heat is required, it is released from the energy - storage medium.
- Advantages: Enables effective heat storage and utilization, improving energy utilization efficiency. It has good adaptability to some situations with unstable energy supply.
- Disadvantages: The energy - storage medium may experience problems such as aging and failure, and thus requires regular maintenance and replacement.