At Wuxi Repicea, we specialize in high-performance heat exchange solutions designed to meet the needs of modern industries. One of the most widely used types is the shell and tube heat exchanger, known for its efficiency, durability, and adaptability in various applications.
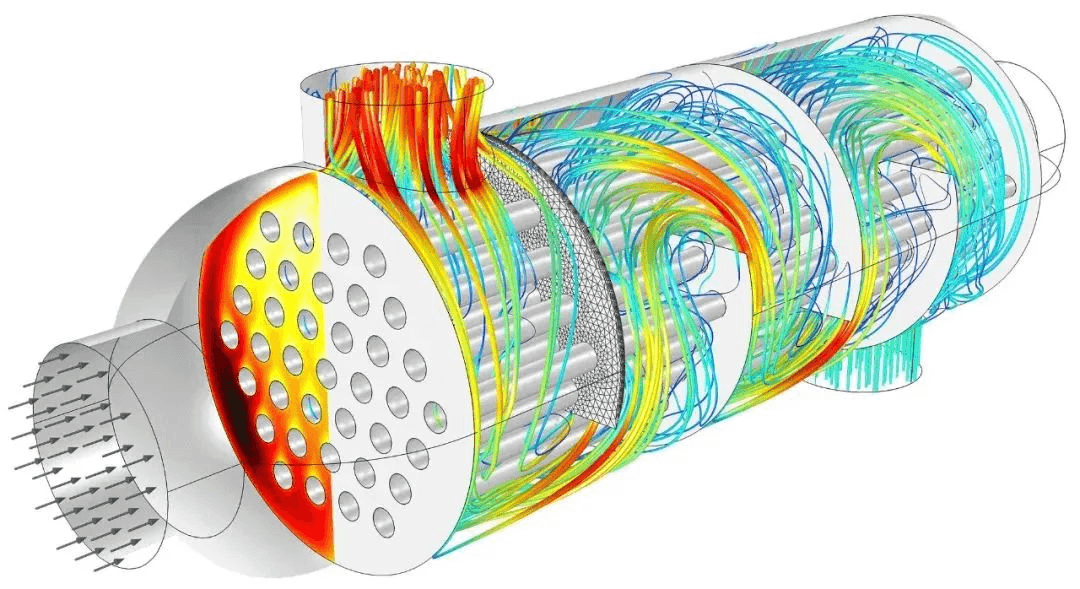
1. What Is a Shell and Tube Heat Exchanger?
Shell and tube heat exchanger—also called a tube bundle heat exchanger—is a wall-type exchanger where heat is transferred between two fluids separated by a tube wall. It consists of a bundle of tubes enclosed within a cylindrical shell, and it’s used for efficient thermal transfer in high-pressure and high-temperature environments.
Key Benefits:
✅Simple structure, reliable operation
✅ Customizable materials for different industrial needs
✅ Ideal for high-temperature and high-pressure conditions
✅ Easy maintenance and cleaning (depending on type)
Given these advantages, shell and tube heat exchangers are widely used in industries like chemical processing, power generation, oil refining, and food production.
2. How Do Shell and Tube Heat Exchangers Work?
These heat exchangers consist of several key components:
Shell: A cylindrical body that houses the tube bundle.
Tube Bundle: A set of tubes that carry one of the working fluids.
Tube Sheets: Plates that hold the tubes in place.
Baffles (Flow Guides): Installed inside the shell to control the fluid flow.
End Chambers: Distribute the fluid across the tubes.
The two fluids in the exchanger follow different paths:
Tube-side fluid flows inside the tubes.
Shell-side fluid flows around the tubes.
To enhance heat transfer, baffles inside the shell direct the fluid flow, creating turbulence that improves efficiency.
💡 Fact: The arrangement of the tubes (triangular vs. square) affects cleaning and performance. Triangular layouts enhance heat transfer, while square layouts allow easier cleaning.
3. Five Types of Shell and Tube Heat Exchangers
1️⃣ Fixed Tube Sheet Heat Exchanger
Best for: Applications with small temperature differences.
The tube bundle is permanently attached to the shell.
- Simple design and low cost.
- Drawback: Cannot expand or contract with temperature changes, leading to stress issues.
To compensate for thermal expansion, an expansion joint can be added.
2️⃣ Floating Head Heat Exchanger
Best for: High-temperature applications requiring frequent maintenance.
One tube sheet is movable, allowing expansion and contraction.
- The entire tube bundle can be removed for cleaning.
- More expensive but highly durable.
- 🔹 Ideal for: Oil refining, power plants, and heavy chemical industries.
3️⃣ U-Tube Heat Exchanger
Best for: Applications with extreme temperature differences.
The tubes are bent into a U-shape, eliminating thermal stress.
- Only one tube sheet is required, simplifying construction.
- Drawback: Cleaning is more challenging due to the curved tubes.
🔹 Ideal for: High-temperature, high-pressure operations.
4️⃣ Packed Gland Heat Exchanger
Best for: Systems with significant temperature variation.
One end of the tube bundle is fixed, while the other is sealed with a packing gland to allow movement.
Allows for easy expansion and contraction, preventing stress damage.
- Drawback: Packing material limits pressure resistance (<4.0 MPa).
🔹 Ideal for: Low-pressure applications that require frequent cleaning.
5️⃣ Kettle Reboiler (Boiling Heat Exchanger)
Best for: Vaporization and distillation processes.
Features a large shell volume to accommodate phase changes.
Used in applications where a liquid is converted to vapor.
- Can withstand high temperatures and pressures.
🔹 Ideal for: Petrochemical refining, power plants, and chemical processing.
4. How to Choose the Right Heat Exchanger
Choosing the right heat exchanger depends on:
✔️ Temperature Difference – If high, opt for floating head or U-tube designs.
✔️ Ease of Cleaning – If fouling is common, consider floating head or packed gland types.
✔️ Space Constraints – U-tube designs are more compact.
✔️ Pressure Requirements – Fixed tube sheet works well under high pressure.
5. Why Choose Wuxi Repicea’s Shell and Tube Heat Exchangers?
At Wuxi Repicea, we manufacture custom-engineered heat exchangers designed to maximize efficiency and longevity. Our products stand out because:
🔥 We use high-quality materials suitable for extreme conditions.
🔩 We offer fully customized solutions to meet industry-specific needs.
🛠️ We prioritize easy maintenance to reduce downtime.
📈 Our designs enhance heat transfer efficiency, saving energy costs.
🚀 Need a reliable heat exchanger? Contact Wuxi Repicea today!